デジタルトランスフォーメーションは、企業変革力を飛躍的に増幅させるものである。
なぜ?と思われる方が多いと思います。企業変革力を高める必要性や、どのように高めればよいのか、よくわからない。投資した効果や価値を見出せない、と思われていると思います。
デジタル化によって、社内業務の効率化を行っただけでは、費用対効果は少なめではないか。と思われていて正解でしょう。これだけでは投資する価値も薄れてしまいます。
投資した価値は、この次にあります。投資して得た効率化によって、得たリソース(ヒト、モノ、カネ)や工数、時間などを顧客のため、社会のため、社会貢献のために、何をどのようにしていくか?
この何をどのようにするかが、付加価値に繋がっていきます。
付加価値は、人件費+減価償却費+営業利益です。
この式から言えることは、営業利益を増大させることになります。人件費は優秀な社員を雇用し、または、外部委託して、減価償却費は優れた設備やデジタル化のためのシステムやアプリケーションを導入することで、今までより一つ上のサービスやできなかったことができるようになるので、顧客満足度の向上も期待できます。
そして、デジタル化によって、業務に関するデータが蓄積されます。このデータを統計・分析することで、勘に頼っていたことの裏付けや実は違っていたことを関係者で共有できるようになっていきます。熟練社員の技術の見える化による継承も可能になります。人材不足、後継者問題、人手不足にもデジタル化によって解決していけます。
データの統計・分析を活用することで、隠れていた課題があぶり出されて顔を出したり、新たな課題が明確になり、課題解決を重ねていくことで、企業変革力を高めることに結びついていきます。
デジタル技術は強力な武器になると言われている所以になります。
VUCAの概要のUncertainty(不確実性)に関連する資料が政府から発行されています。
2020年版ものづくり白書
第1部 ものづくり基盤技術の現状と課題
第3節 製造業の企業変革力を強化するデジタルトランスフォーメーション(DX)の推進
以下に抜粋してご紹介します。
2020年版ものづくり白書 第1部 ものづくり基盤技術の現状と課題 総論のなかで、以下のように記載されています。
② 企業変革力を強化するデジタルトランスフォーメーション推進の必要
IoT や AI といったデジタル技術は、生産性の向上や安定稼働、品質の確保など、製造業に様々な恩恵を与える。しかし、今回のものづくり白書では、デジタル技術が企業変革力を高める上での強力な武器であるという点を最大限に強調する。
例えば、脅威や機会をいち早く感知するのに有効なリアルタイム・データの収集や AI の活用、機会を逃さず捕捉するための変種変量生産やサービタイゼーション、組織や企業文化を柔軟なものへと変容させるデジタルトランスフォーメーションは、企業変革力を飛躍的に増幅させるものである。
特に、新型コロナウイルス感染症の感染拡大を受けて、臨時休校や医療現場での感染予防の観点から、遠隔教育や遠隔医療など、リモート化の取組を求めるニーズが高まっており、我が国のデジタルトランスフォーメーションの必要性が加速している。このような取組によって、将来の感染症に対して強靱な経済構造を構築し、中長期的に持続的な成長軌道を確実なものとする必要がある。
このように、単に新しいデジタル技術を導入するというのではなく、それを企業変革力の強化に結びつけられる企業が、この不確実性の時代における競争で優位なポジションを得ることができる。しかし、今回の白書の分析では、我が国製造業は、IT投資目的の消極性、データの収集・活用の停滞、老朽化した基幹系システムの存在といった課題を抱えていることを明らかにしている。
目次
第3節 製造業の企業変革力を強化するデジタルトランスフォーメーション(DX)の推進
1 日本の製造業のデジタルトランスフォーメーションにおける課題
(1)製造業におけるデジタル技術のインパクト
ドイツの “インダストリー 4.0”、フランスの “未来の産業(Industrie du Futur)”、中国の “中国製造 2025” など、世界の主要各国が、第四次産業革命への対応を進めている中、日本もまた、目指すべき社会の姿として “Society 5.0” を掲げ、さらに2017 年 3 月、我が国の産業が目指すべき姿として“Connected Industries(コネクテッドインダストリーズ)” というコンセプトを提唱し、世界に向けて発信した。
“Connected Industries” とは、データを介して、機械、技術、人など様々なものがつながることで、新たな付加価値創出と社会課題の解決を目指す産業の在り方である。このコンセプトを具体化する上でカギとなるのは、IoT や AI を始めとする最新のデジタル技
術である。このようなデジタル技術は、より具体的には、次のようにして製造業に大きな変革(デジタルトランスフォーメーション)をもたらす。
そもそも製造工程には、大まかに言って、研究開発-製品設計-工程設計―生産などの連鎖である「エンジニアリングチェーン」と、受発注-生産管理-生産-流通・販売-アフターサービスなどの連鎖である「サプライチェーン」がある。製品や生産技術に関するデータは、この2つのチェーンを通って流れ、結びつき、そして付加価値を生み出す。
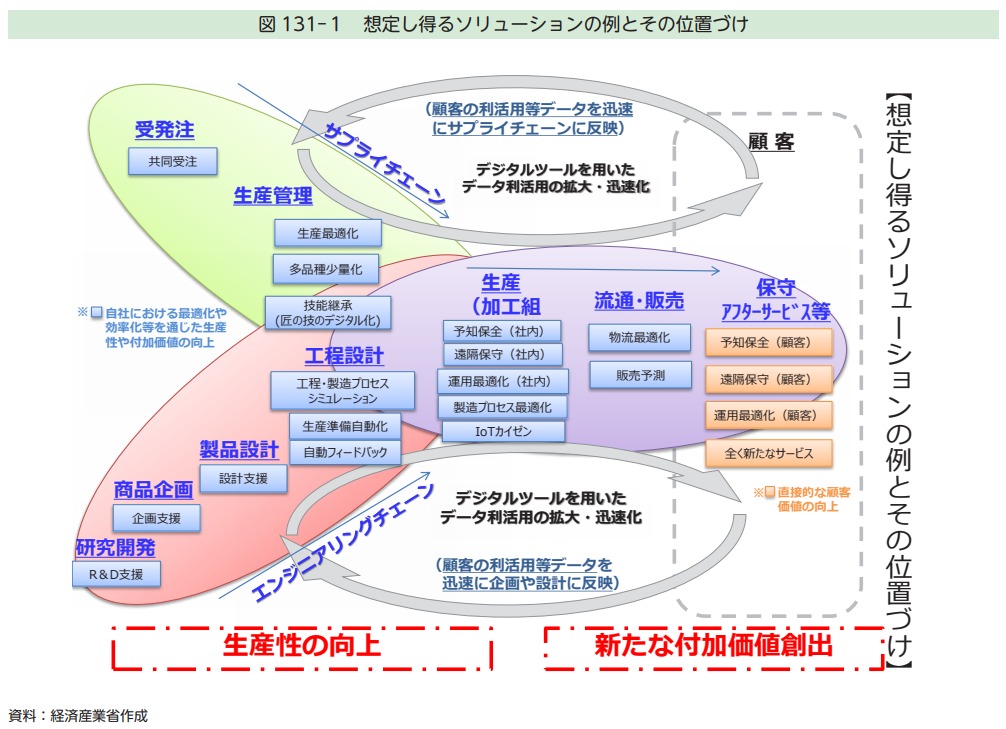
IoT を始めとする最新のデジタル技術は、双方のチェーンの各所において、データの利活用を進める優れたソリューションを提供し、製造業に画期的な革新をもたらす。
例えば、エンジニアリングチェーンにおいては、強化された計算能力や AI などを研究開発等に活用する「R&D 支援」、顧客の仕様データなどを分析することによる「企画支援」、モデルベース開発を始めとする「設計支援」などがある。
サプライチェーンにおいては、工場ごとの繁閑期の平準化などを可能とする「共同受注」、デジタル化により匠の技の継承を容易にする「技能継承」、サプライチェーン連携などによる「物流最適化」、顧客の使用データなどを分析することによる「販売予測」、設備・機器の「予知保全」「遠隔保守」などがある。
そして最も重要なことは、エンジニアリングチェーンとサプライチェーンをシームレスにつなぐことである。これにより、「生産最適化」さらには「マスカスタマイゼーション」が可能になるだけでなく、「サービタイゼーション」あるいは「ことづくり」といった新たなビジネスの設計もより容易になる。
このデジタル技術によるエンジニアリングチェーンとサプライチェーンの連携については、2.において更に検討する。
(2)国内製造業企業のデータ活用の遅れ
以上で述べたエンジニアリングチェーンとサプライチェーンの強化及び両者の連携にはデジタル技術が不可欠である。このような製造業における2つのチェーンにソリューションを提供するデジタル技術について、日本企業の導入状況を確認したい。
国内製造業に対して、生産プロセスに関する設備の稼働状況等のデータ収集を行っているかを尋ねたところ、データ収集を行っている企業の割合は、2018 年12 月調査時の 58.0%よりも7%減少し、51.0%となった(2019 年 12 月)(図 131-2)
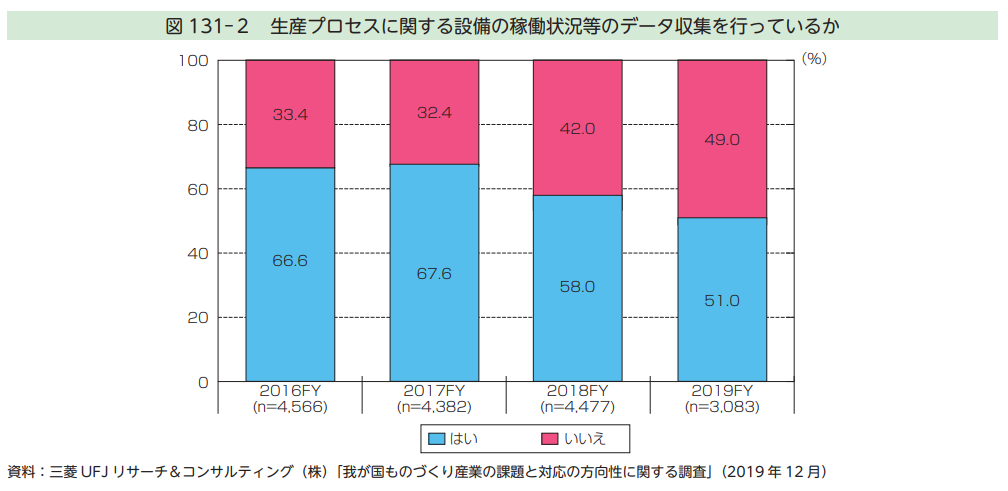
さらに、センサーや IT を活用して個別工程、製造工程全般、人員のそれぞれの稼働状況の「見える化」によるプロセス改善等に取り組んでいるか(図 131-3・4・5・6)、海外工場において国内工場と同じかそれ以上の生産プロセスにかかるデータ等の収集・活用を実施しているか(図 131-7)について尋ねたところ、いずれについても、大きな進展は見られなかった。
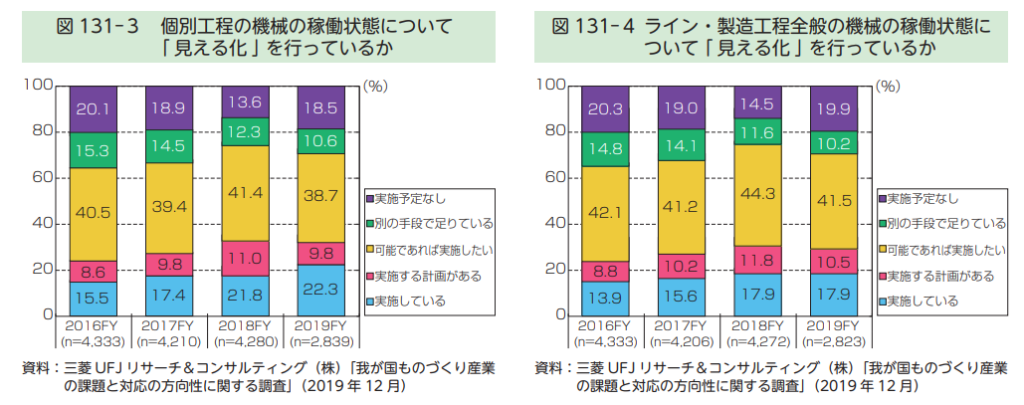
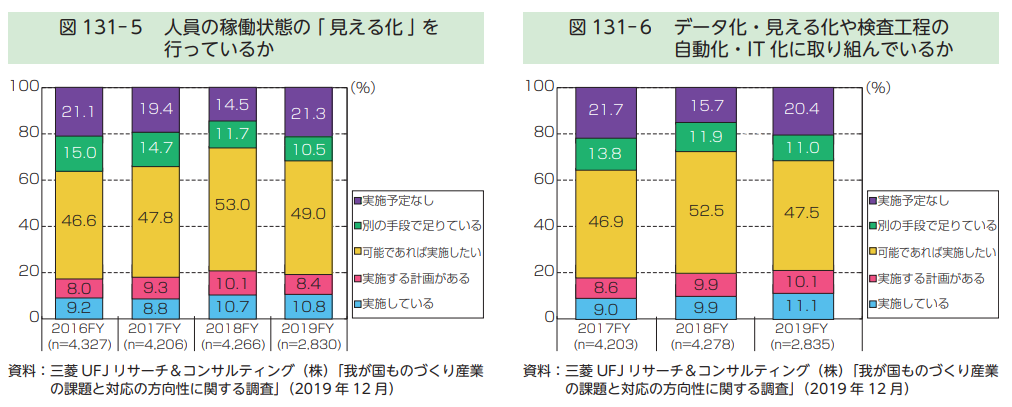
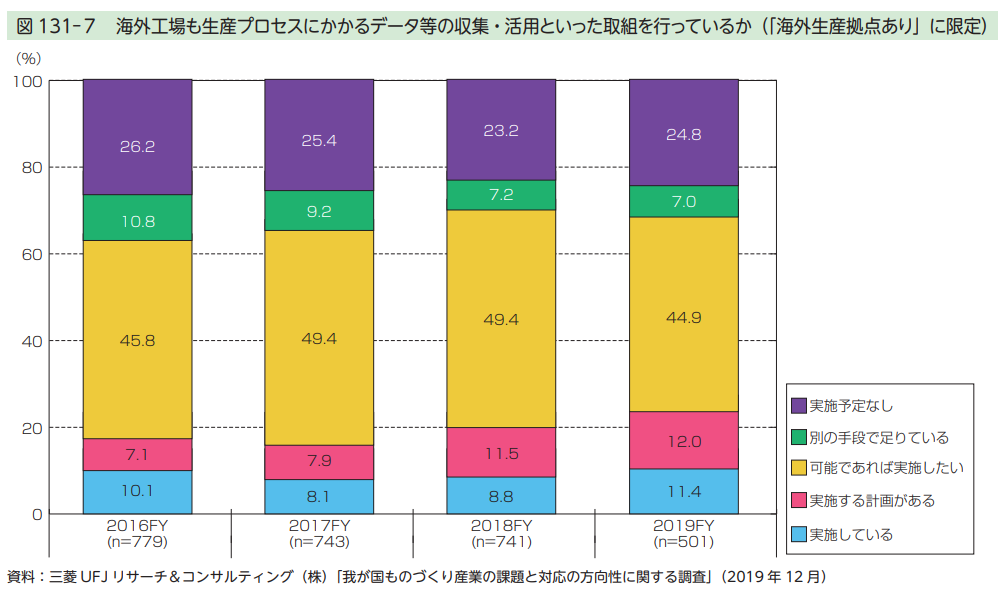
特に、2019 年版ものづくり白書においても課題として挙げた顧客目線でのビジネス展開に関しても、データ連携が進んでいないことが明らかとなった。複数部門間での情報・データ共有について、販売後の製品の動向や顧客の声を設計開発や生産改善に活用しているかどうかを確認したところ、「実施している」と回答した企業は前回調査時(2017 年度)と比べて 15.8%から 8.4%へと大きく減少した(図 131-8)
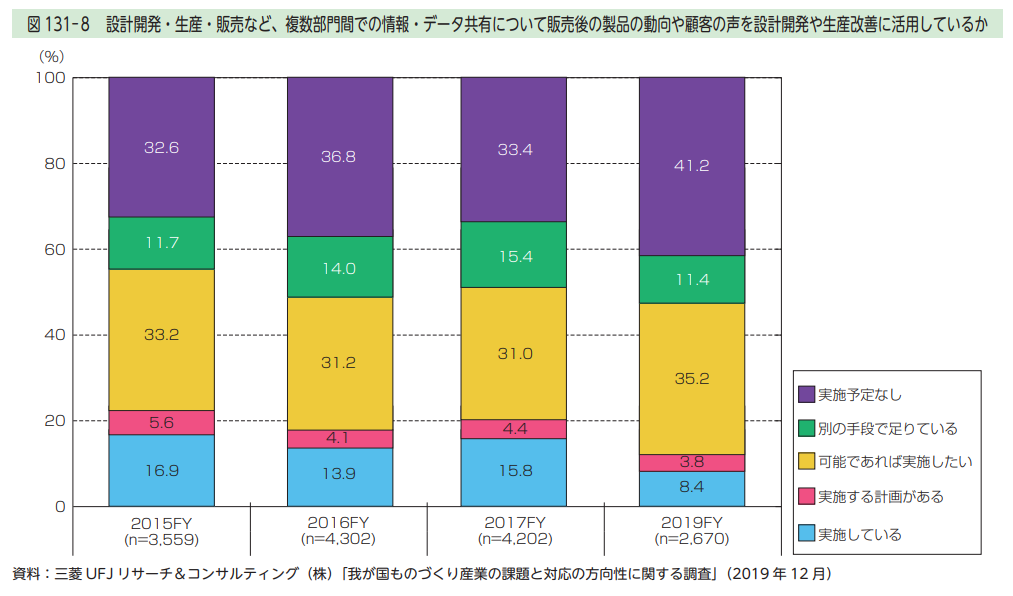
このようなことから、我が国製造業におけるデータ収集・活用の取組はここのところ足踏み感が見られ、新型コロナウイルス感染症の感染拡大を始めとする不確実性の高まりも相まって、今後の投資についても停滞することが懸念される。
(3)「2025年の崖」
製造業のデジタルトランスフォーメーションを阻害し、ダイナミック・ケイパビリティを低下させるリスクとして見落としてはならないものの一つに、基幹系システムの問題がある。
経済産業省「デジタルトランスフォーメーションに向けた研究会」の報告書「DX レポート~ IT システム「2025 年の崖」の克服と DX の本格的な展開~」(平成 30 年 9 月 7 日)(図 131-9・10)は、日本企業の約8割が、いわゆる「レガシーシステム」(複雑化・老朽化・ブラックボックス化した基幹系システム)を抱えていると警鐘を鳴らしている。
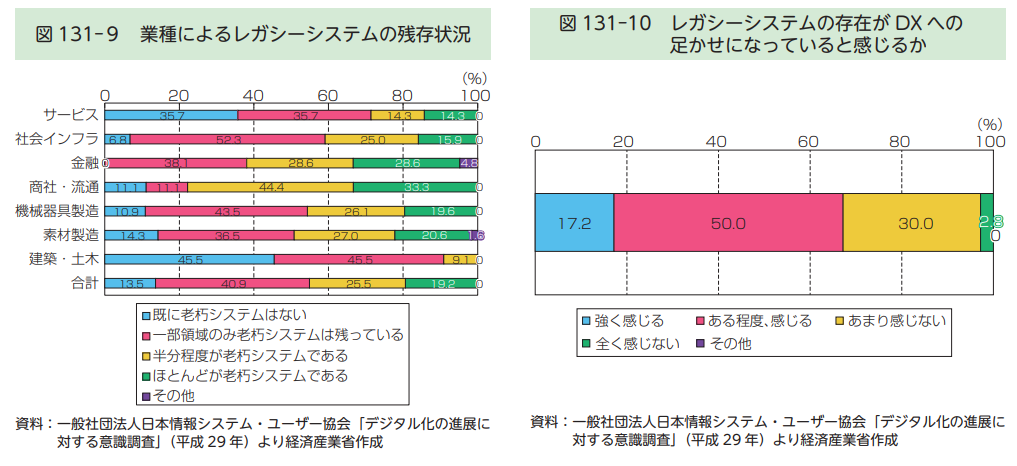
世界規模でデジタルトランスフォーメーションが進む中、「レガシーシステム」が残存している企業では、爆発的に増加するデータを活用しきれず、デジタル競争の敗者となる恐れがある。また、IT システムの運用・保守の担い手が不在になり、多くの「技術的負債」を抱えるとともに、業務基盤そのものの維持・継承が困難になる。
サイバーセキュリティや事故・災害によるシステムトラブルやデータ滅失・流出等のリスクが高まることも予想される。すでに、我が国企業の IT 関連予算の 80%は現行ビジネスの維持・運営(ラン・ザ・ビジネス)に割り当てられており、さらにラン・ザ・ビジネス予算が 90%以上を占める企業も 40%を超えている。それは、裏を返せば、バリュー・アップのための IT 投資が IT 予算の2割以下に過ぎないということを意味する。
DX レポートは、「レガシーシステム」が残存した場合、2025 年までに予想される IT 人材の引退やサポート終了等によるリスクの高まり等に伴う経済損失は、2025 年以降、最大 12 兆円/年(現在の約3倍)に上る可能性があると指摘し、これを「2025 年の崖」と呼んでいる。この「2025 年の崖」の問題は、我が国の製造業においても存在しており、その解決は喫緊の課題である。
レガシーシステムは、製造業のダイナミック・ケイパビリティとも関係している。というのも、レガシーシステムは、大量のデータの利活用を困難にする、あるいはシステムの維持・運営費が技術的負債として重くのしかかるといった理由により、ダイナミック・ケイパビリティを制約するからである。
IT 投資の目的に関する調査結果によれば、オーディナリー・ケイパビリティ重視の企業は、「旧来型の基幹システムの更新や維持メンテナンス」が75.0%を占めており、ダイナミック・ケイパビリティ重視の企業の 47.1%に比べて、圧倒的に高い(図131-11 注2)。
ダイナミック・ケイパビリティを重視する企業ほど、技術的負債を圧縮し、バリュー・アップにより多くの IT 予算を振り向けているものと考えられる。
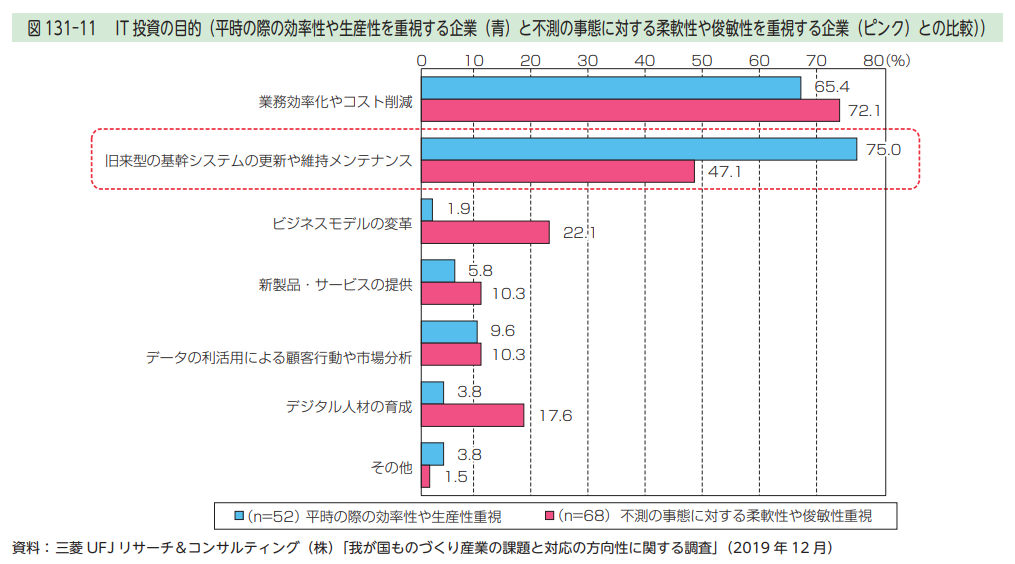
2 設計力強化戦略
(1)品質・コストの8割は設計で決まる
次に、デジタル技術によるエンジニアリングチェーンとサプライチェーンの連携の意義について議論するが、その前提として、エンジニアリングチェーンの重要性について、改めて確認する必要がある。
製造業では、製品の品質とコストの8割は、設計段階で決まると言われてきた。
図 132-1は、仕様変更の自由度と品質・コストの確定度を示したものである。開発が進むに従って製造設備などが確定していくため、仕様変更の自由度は低下し、設計が完了した後の仕様変更の余地は極めて限定的なものとなる。その結果、仕様変更の自由度が高い設計段階で、製品の品質とコストの8割程度が決まることになるのである。
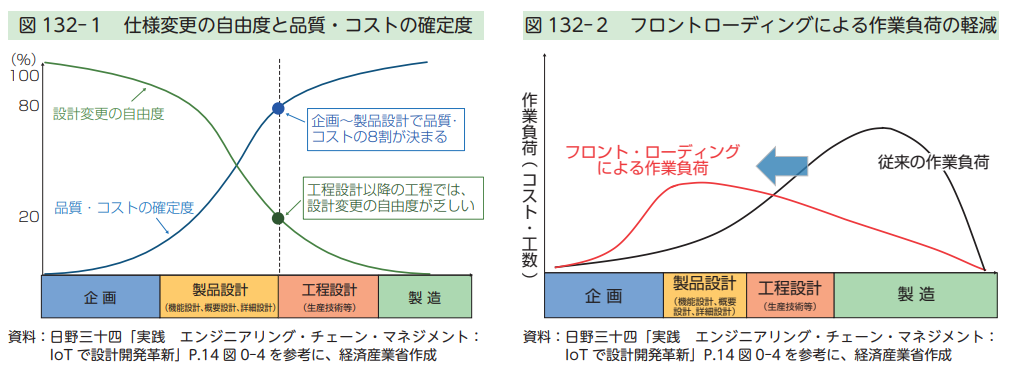
このため、できるだけ開発の初期段階であるエンジニアリングチェーンに資源を集中的に投入すること(「フロントローディング」により、問題点の早期発見、品質向上、後工程での手戻りによるムダを少なくすることが決定的に重要になる(図 132-2)。
その上、近年、グローバル化、顧客の製品機能要求の高度化・多様化、環境制約・資源制約の先鋭化といった傾向が高まっている。特に、2015 年9月の国連サミットにおいて「持続可能な開発目標(SDGs)」が採択されたことで、企業が果たすべき社会的役割に注目が集まり、我が国製造業企業にも対応が求められている。製品に対する機能要求が高まる一方で、制約条件が厳しくなるのであれば、製品は一層複雑化することにならざるを得ない。
また、製品に占める制御ソフトウェアの比率が高まっていることも、製品の複雑化を招いている。この傾向は自動車において特に顕著である。自動車ソフトウェアのコード数は、2000 年時点では 100 万行程度であったが、現在では1億行を超えている。
F-35 戦闘機が 2000 万行、Microsoft Office 2013が 4,400 万行と言われているので、自動車ソフトウェアの複雑さは突出している。このように製品が複雑化していけばいくほど、エンジニアリングチェーンに掛かる負荷はより大きなものとなる。
すなわち、製品の複雑化が進めば進むほどに、それに対応できるエンジニアリング能力の高さこそが、製造業の競争力を左右するといえる。
さらに、第2節で論じたように、近年、世界的に不確実性が高まっており、我が国の製造業は、この不確実性にも対応しなければならなくなっている。より具体的にいえば、想定外の突発的な環境や状況の変化が発生した場合、製品の仕様を早急に変更しなければならないというリスクにさらされているのである。
例えば、このような事態に対しては、仕様変更の自由度が高い設計段階において対応せざるを得ず、しかも可能な限り迅速に対応することが重要である。さらに仕様変更に対応する「製品設計」のみならず、仕様を変更した製品を効率的に製造できるよう、製造工程を迅速かつ自在に変更するための「工程設計」の能力も必要となる。
このように、不確実性に対応するには、製品設計と工程設計の双方を含むエンジニアリングに高い能力があることが求められる。エンジニアリングの能力は、製造業が不確実性に対応するダイナミック・ケイパビリティの中核を占めるものといえる。
(2)我が国の製造業のエンジニアリングチェーンの現状と課題
それでは、我が国製造業のエンジニアリングチェーンは現在どのような状態にあるのだろうか。
2019 年 12 月に国内製造業に対して実施されたアンケートによれば、エンジニアリングチェーンの上流に当たる製品設計力のここ5年間での変化の状況について、約4割が向上していると答えたものの、半数以上が「あまり変化は無い」と回答している(図 132-
3)。
製品設計のリードタイムに関しても同様で、約4割が短くなっていると回答した一方で、半数以上が「あまり変わらない」としている(図 132-4)。製品設計のリードタイム短縮を図るための取組として重視しているものを確認すると、半数以上が「生産技術、製造、調達といった他部門との連携促進」と回答しており、設計力の強化に向けては他部門との連携が重視されている(図 132-5)
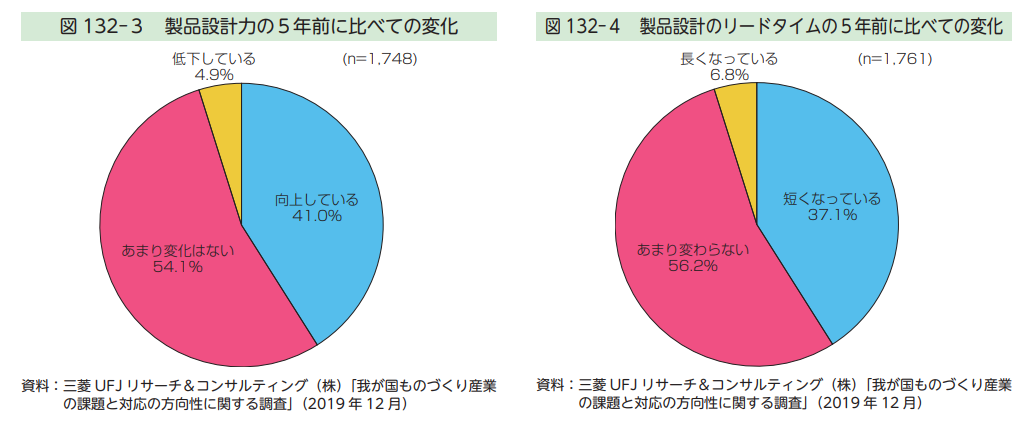
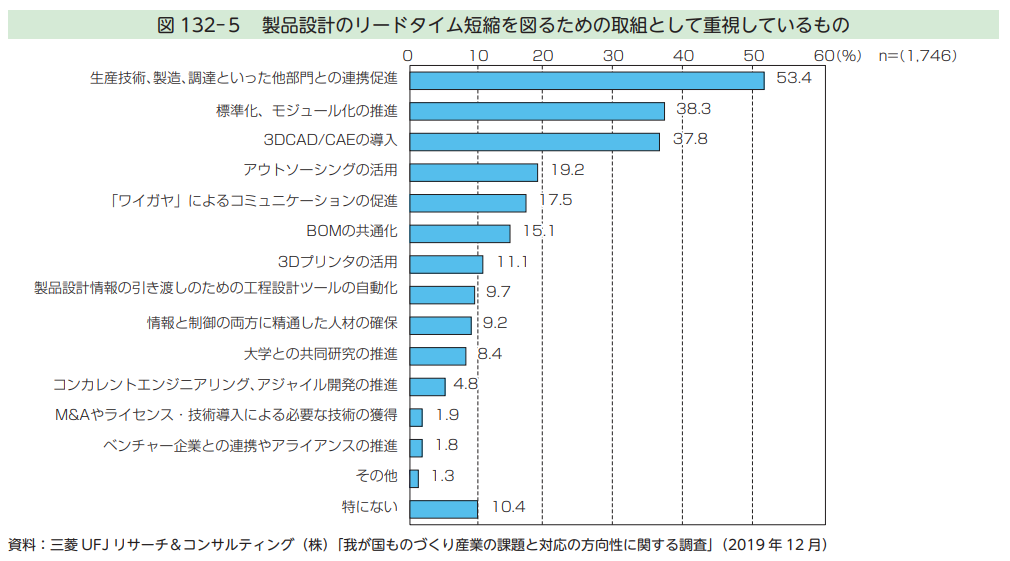
また、国内製造業に対して工程設計(生産技術)力のここ5年間での変化について尋ねたところ、36.9%が「向上している」、58.8% が「あまり変化はない」、4.3%が「低下している」と回答した(図132-6)。
工程設計力が「向上している」と回答した企業に対してその要因を確認したところ、「生産技術、製造、調達といった他部門との連携強化」と回答した企業が最も多く 79.2%を占め、「営業、アフターサービスなどから顧客ニーズのフィードバックを強化(26.5%)」「デジタル人材の育成、確保(22.5%)」が続いている(図 132-7)。
一方、工程設計力が「低下している」と回答した企業についても同様にその要因を確認すると、「ベテラン技術者の減少(79.4%)」、「製造現場との連携不足(30.9%)」、「属人的な設計プロセス(25.0%)」、「間接部門の人員削減(19.1%)」が上位に挙がっている(図 132-8)。
この結果から、工程設計力の維持が熟練者の技に頼りがちで、その技術を後継に引き継ぐことが課題となっている様子がうかがえる。また、他部門との連携は、向上・低下双方の要因として上位に挙げられており、他部門との協調が工程設計力強化の鍵であることが分かる。
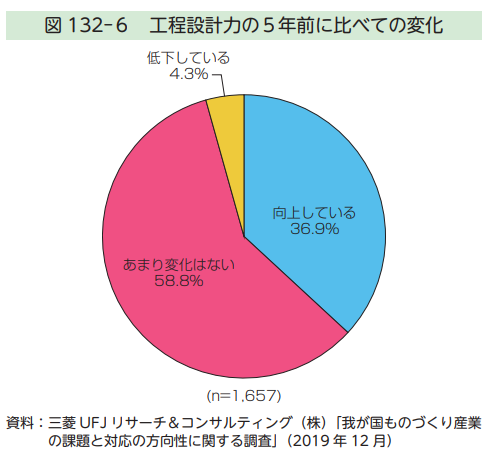
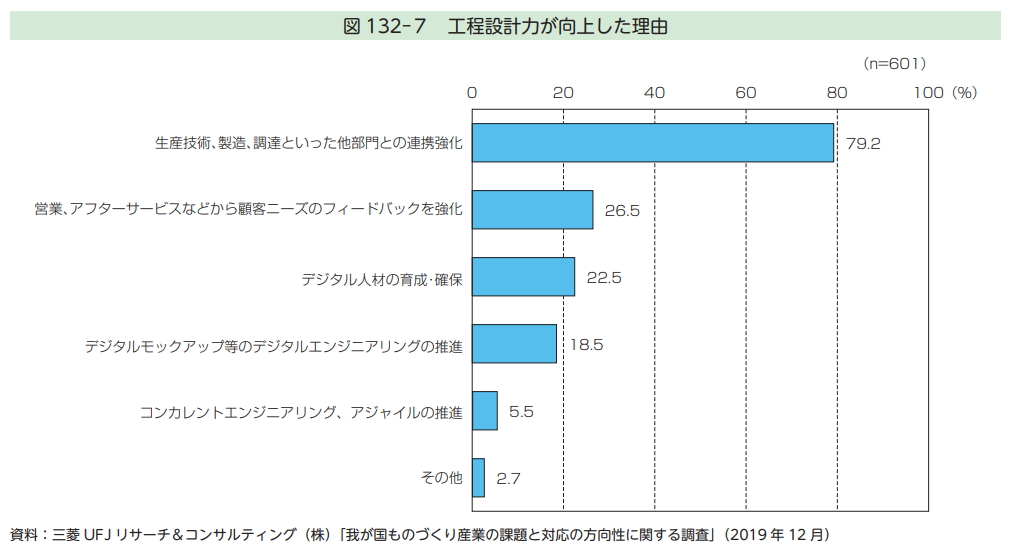
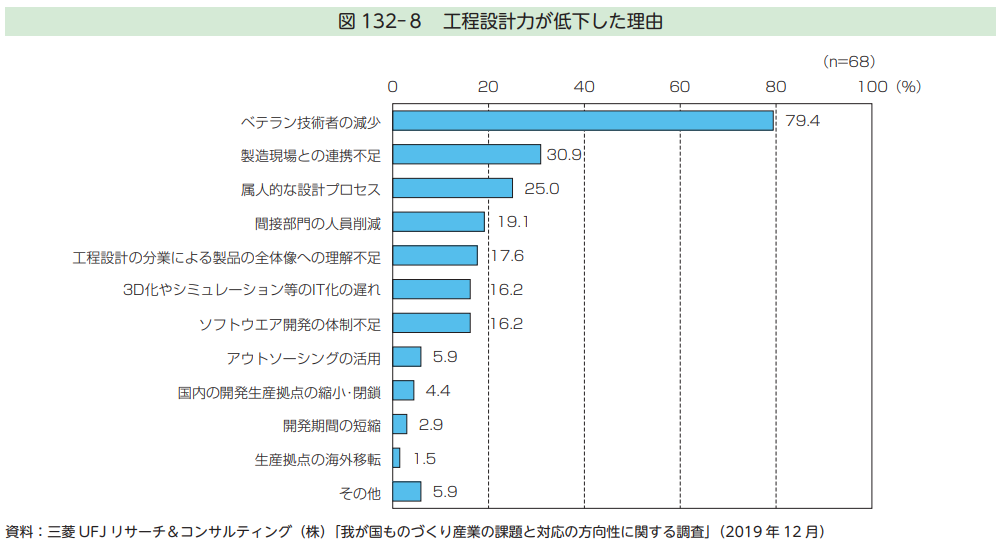
そこで、国内製造業における製品設計、工程設計、製造等の部門間の連携状況を見ると、「ある程度連携がとれている」と回答した者が 72.1%を占め、自社の部門間連携に対して課題と感じていない者が多数を占めている(図 132-9)。
一方で、「あまり連携がとれていない」もしくは「連携がとれていない」と回答し、部門間連携に課題を感じている企業に対して、それにより生じる課題や問題を聞くと、「品質不良が発生する(55.5%)」「設計変更が製造に伝わらないことがある(42.8%)」「正確なコスト予測ができない(39.4%)」といった回答が上位に挙がった(図 132-10)。
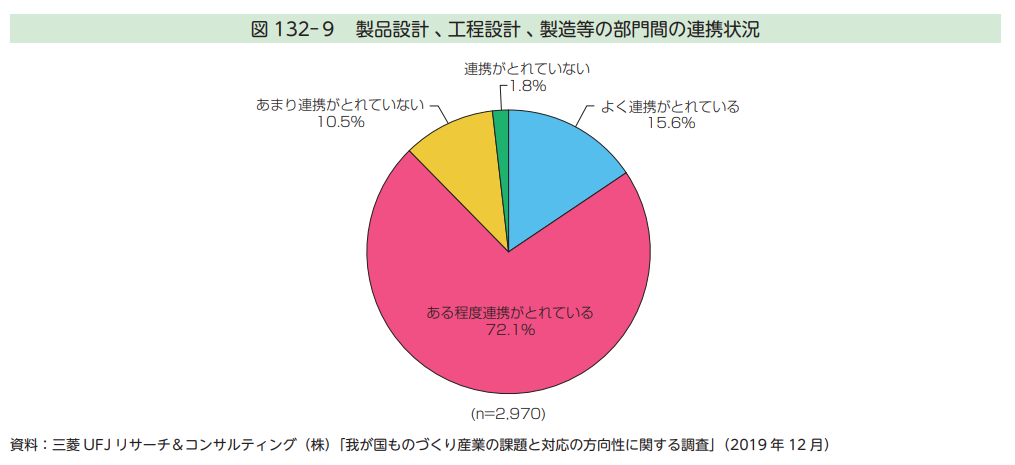
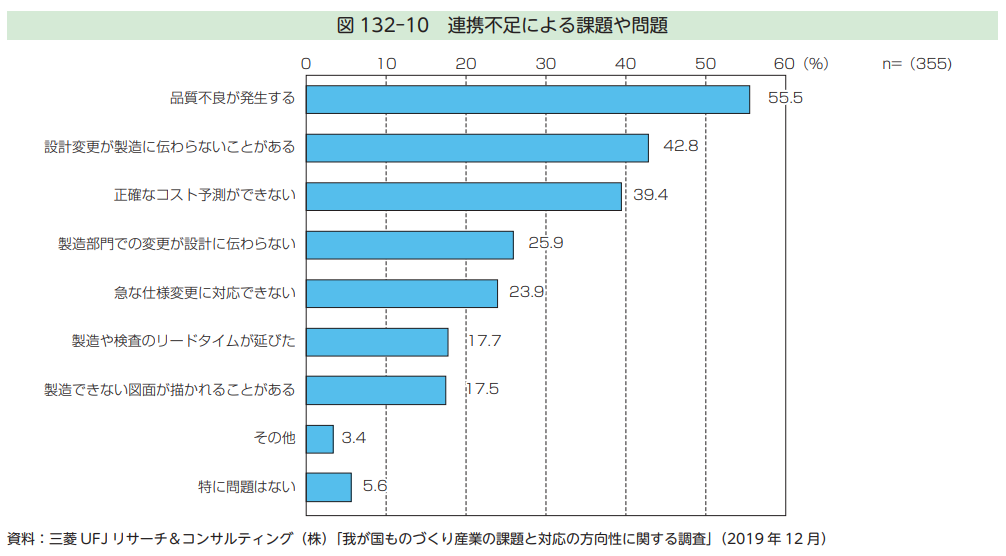
我が国製造業における品質不正の問題については、2017 年 10 月以降、製品検査データの書き換えなどの不正事案が複数発覚した。
品質保証体制の在り方は企業の競争力に直結する経営問題であり、また、サプライチェーン等を考慮すれば、我が国製造業全体の競争力にも影響を及ぼしかねない。部門間における連携が不足していることが品質不良につながっており、早急な解決が必要である。
また、製品設計力や工程設計力の伸びと部門間の連携状況との関係を見ても、部門間の連携がとれている企業ほど、製品設計力、工程設計力が向上する傾向にある(図 132-11・12)
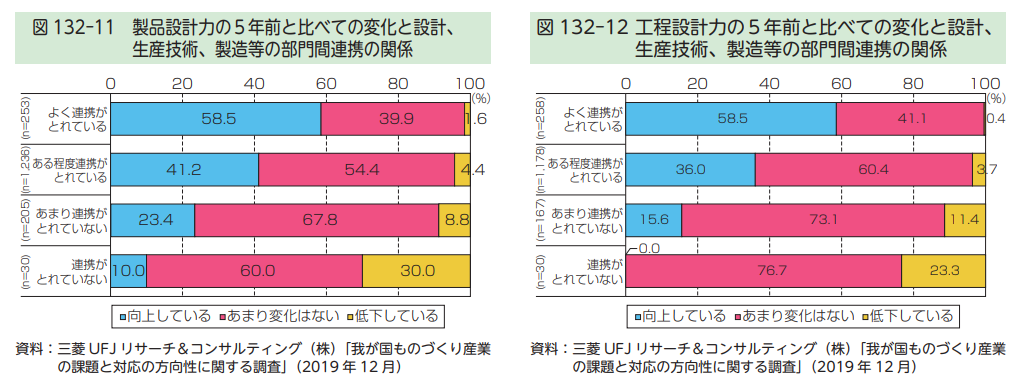
図 132-12 工程設計力の5年前と比べての変化と設計、生産技術、製造等の部門間連携の関係
(3)部門間・企業間のデータ連携
すでに述べたとおり、エンジニアリングチェーンを強化する上では、設計、製造、調達といった各部門との連携を強化することが有効である。
しかし、実際には、企業内部において、設計部門と製造部門の間のコミュニケーションが十分に行われていない場合がある。また、設計部門と製造部門が、それぞれ異なるIT ベンダーから異なる IT システムを導入しているため、両部門のシステムの連携が必ずしもうまくいっていないという場合もある。
設計部門と製造部門の連携が不十分な場合には、先ほどのアンケート結果からも推察されるとおり、
・ 設計部門のデータと製造部門のデータの変換処理に膨大な工数や処理時間が掛かる
・ 作業工程・設備・治工具などの製造現場の情報が設計仕様に反映できないために製造現場に過度な負担が掛かる
・ 当初見込まれなかった製造や調達のコストや作業などの情報が設計側に反映されない
・ 設計部門と製造部門の伝達のミスが発生しやすく、両部門間の打ち合わせを頻繁に行わなければならない
などの問題が生じる。これらの問題は、製品の複雑化や不確実性の高まりによっていっそう深刻化し、製造業の競争力にとって致命的なものとなりかねない。
エンジニアリングチェーンとサプライチェーンを連携させるために必要な第一歩は、設計部門が設計を行う上で使用する設計部品表、製造部門が製造を行う上で使用する製造部品表、そして工程設計情報をまとめたものである工程表を結びつけて、各部門がこれらを共有することである。
これにより、設計部門から製造部門、あるいは製造部門から設計部門への双方向の円滑なデータ連携が可能となる。例えば、設計変更による製造現場への影響範囲を確認しながら設計を行ったり、あるいは生産管理を変更したりすることが容易になる。さらに、製造部門から、原価実績情報も含めた製造情報を設計部門にフィードバックすることで、設計段階で精度の高い原価企画やシミュレーションを行うことも可能になる。
加えて、部門を超えたデータ連携により部門間の連携が強化されることで、品質不良の削減につながり、ひいては我が国製造業における品質保証体制強化と生産性向上の両立を実現することが期待される。
なお、第2節2.(4)で論じた「柔軟な組織」は、権限や部門を横断した連携やコミュニケーションをより円滑に行うことができ、高いダイナミック・ケイパビリティを発揮できる組織である。部品表や工程表の整備は、そうした部門を超えたデータ連携を容易にすることで、組織を柔軟にし、ダイナミック・ケイパビリティを高めるものである。
さらに、このようなデータの連携と双方向のコミュニケーションは、設計部門と製造部門のみならず、企業全体、さらには企業組織の枠をも超えてサプライヤーや顧客などの間でも実現することで、いっそう大きな威力を発揮するであろう。
このことは、第2節2.(5)で論じたサプライチェーンの柔軟性等を高める上でも、極めて重要である。というのも、仮に不測の事態が勃発して、ある国の生産拠点が停止せざるを得なくなった場合、生産を別の工場において迅速に代替できれば、供給途絶は回避できる。しかし、設計部品表、製造部品表、工程表が統一的に整備され、共有されていない場合は、代替生産を開始する際に部品表から調整しなければならないため、膨大な人員と作業を要することになる。これでは、柔軟かつ迅速な代替生産を行うことは不可能である。
このように、サプライチェーンの柔軟性等を高め、ダイナミック・ケイパビリティを強化するためには、実は、部品表や工程表を整備し、エンジニアリングチェーンとサプライチェーンを連携させておかなければならないのである。
新型コロナウイルス感染症の感染拡大を契機に、グローバル・サプライチェーンの強化の必要性が改めて認識されているが、強靭なサプライチェーンを構築するためにも、部品表や工程表を整備し、エンジニアリングチェーンを強化することが不可欠なのである。
(4)バーチャル・エンジニアリング
1990 年代半ば以降、製造業の設計現場に3DCAD(Computer Aided Design)の導入が始まった。
2000 年以降になると、CAM(Computer AidedManufacturing)に CAE(Computer AidedEngineering)が加わるようになり、さらに PDM(Product Data Management)によって、設計・製造・解析の各データを同期させて一体に検討する「バーチャル・エンジニアリング」の環境が整備されていった。最近では、これに IoT や AI が加わり、バーチャル・エンジニアリングは更なる進化を遂げつつある。
このバーチャル・エンジニアリングにより、企画、設計、製造、営業、品質、認証等の各分野の専門家、さらにはサプライヤーや一部顧客までも含めて、3D図面を用いて同期的・一体的に製品開発に参加することができる協業の場が実現する。
また、バーチャル・エンジニアリングを用いることで、構想設計の段階で、検証も含めた詳細設計までが可能になり、リアルな試作の前に全ての仕様を決めることができるので、製品開発のリードタイムは、大幅に短縮することとなる。このようなエンジニアリングの手法は、「コンカレント・エンジニアリング」「サイマルテニアス・エンジニアリング」とも呼ばれる。
ダイナミック・ケイパビリティ論に即していえば、バーチャル・エンジニアリングは、機会を捉え、既存の組織内外の資産・知識・技術を再構成して競争力を獲得する「捕捉」の能力を著しく高め、開発リードタイムを極限まで短縮化する。
こうして、バーチャル・エンジニアリングは、不測の事態に迅速に対応する能力であるダイナミック・ケイパビリティを著しく高めるのである。
従来、日本の製造業は、製造現場の技術力(いわゆる「匠の技」)が非常に高く、それが競争力の源泉となっていた。このため、設計部門から送られてきた設計図面が多少不備であっても、製造部門の技術者が、設計図面を細かく修正したり、詳細部分を設計したりすることができた。日本の製造業では、生産設備を考慮に入れた量産品質の高い最適仕様の設定は、設計部門ではなく、製造部門において行われる傾向にあったのである。
しかし、近年、製品の複雑化が進み、さらには不確実性が高まる中で不測の事態への俊敏な対応も必要になる中では、これまでのように、詳細設計まで製造現場の技術力に過度に依存することは、極めて難しくなっている。加えて、近年、生産年齢人口の減少等により、熟練技術者が減り、生産現場の技術力の維持・向上にも支障を来しつつある。このようなことから、製造業が競争力を維持し強化する上では、バーチャル・エンジニアリングは大きな役割を果たすものと考えられる。
ところが、我が国の製造業では、バーチャル・エンジニアリングが進んでいないことが、今回の調査で浮き彫りとなった。
バーチャル・エンジニアリングでは、3DCAD を用いて設計図面を描くだけにとどまるものではなく、設計情報の受け渡しも3Dデータで行うことが基本となる。ところが、3D データのみで設計を行っているのはわずか 17.0%にとどまっている(図 132-13)ことに加え、協力企業への設計指示の半数以上が未だに図面で行われ、3D データによる指示は 15.7%に過ぎない(図 132-14)。また、3D データによる指示を行わない理由の約半数が、「主な設計手法が3Dではないため」と答えている(図 132-15)。
関連して、一般社団法人日本自動車工業会が同工業会に加盟する自動車会社に対して行った調査(図132-16)によれば、全体的に、2D 図主体から3D図主体への移行は停滞しており、直近では、3D 図から2D 図への回帰の傾向すら現れている。また、3D 図面化を進めようとしている企業と、2D 図主体を維持しようとする企業との二極化が拡大している。
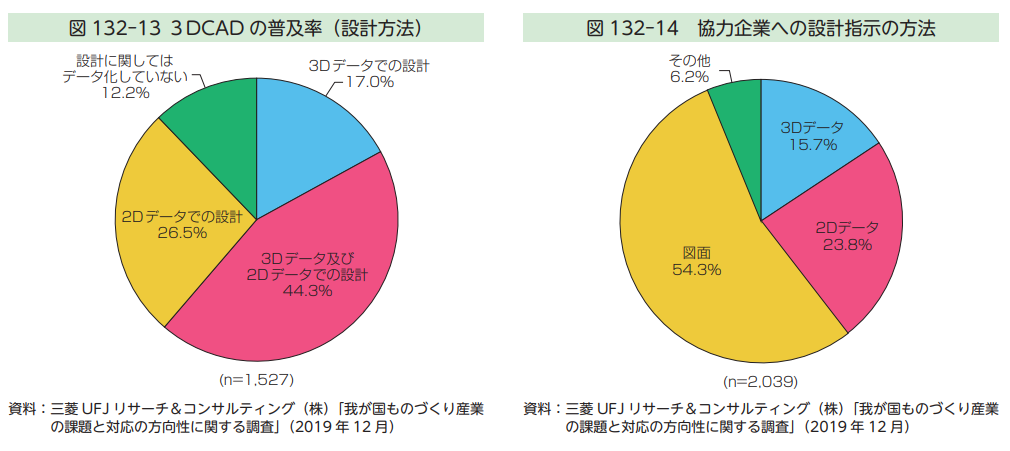
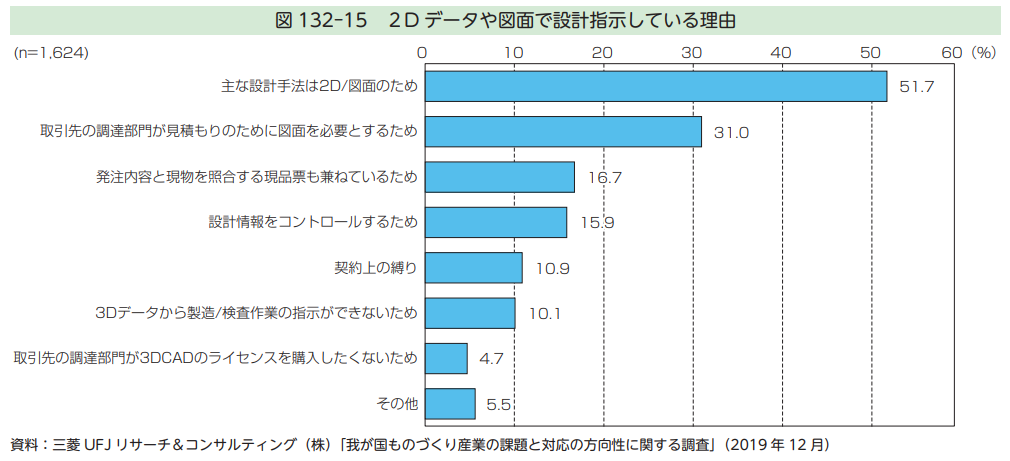
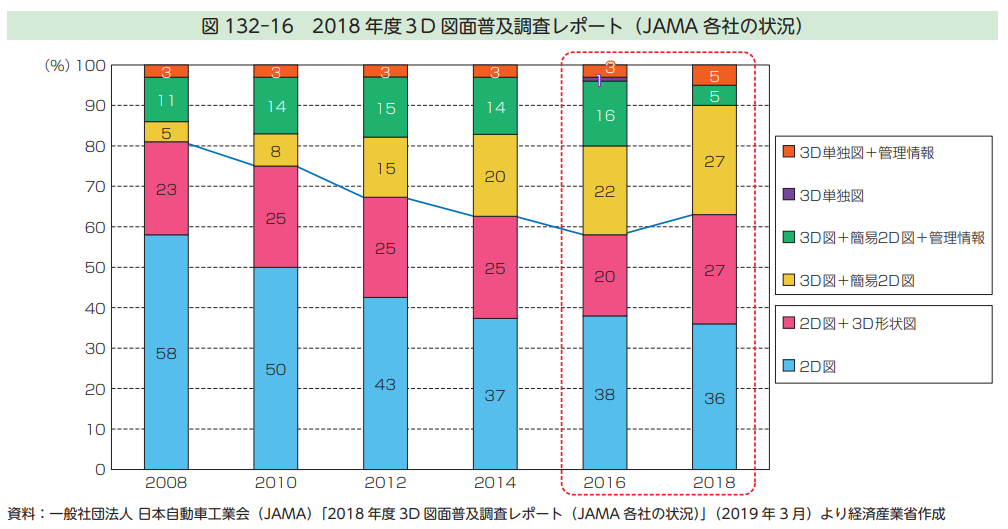
しかし、3DCAD を利用しバーチャル・エンジニアリングを進めることはエンジニアリングチェーンの強化に不可欠である。
アンケートを見ても、3DCAD を利用した設計が進んでいる企業ほど、製品設計力が向上し、製品設計のリードタイムが短縮している(図 132-17・18)。さらに、工程設計力も向上している(図 132-19)。アンケートの結果からも、3DCAD の利用がエンジニアリングチェーンの強化に大きく貢献することが分かる。
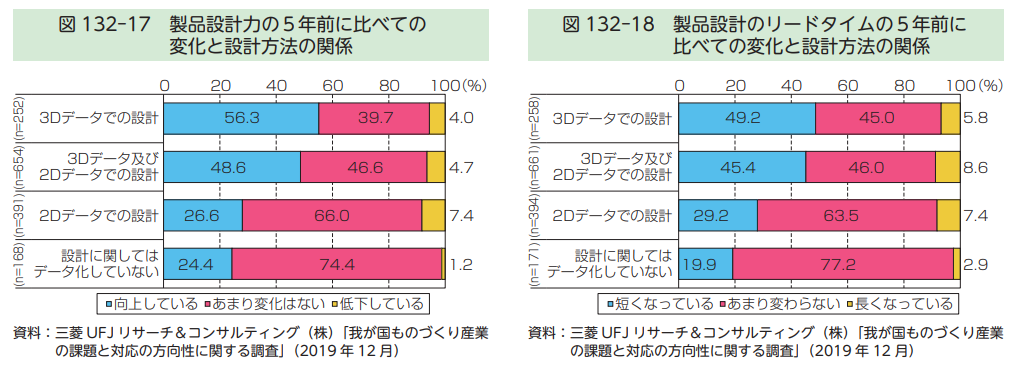
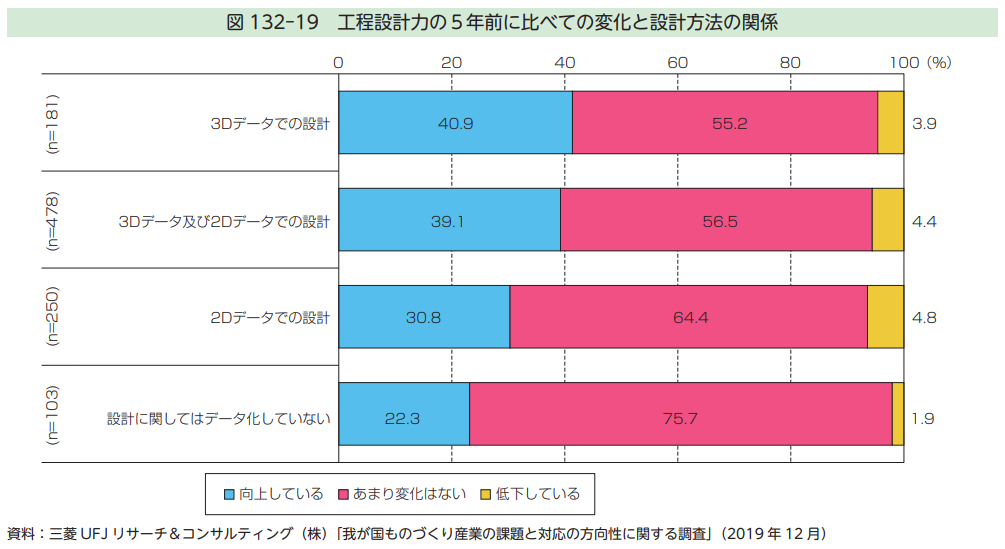
以上で見てきたように、我が国の製造業では3Dによる設計が未だに普及しておらず、バーチャル・エンジニアリングの体制が整っていない。不確実性が高まり、製造業のダイナミック・ケイパビリティの重要性が増している中で、このバーチャル・エンジニアリング環境の遅れは、我が国製造業のアキレス腱となりかねないと言っても過言ではない。
(5)マテリアルズ・インフォマティクスの波
2.(4)のバーチャル・エンジニアリングは、主として、自動車産業や電機産業などのディスクリート系(加工組立系)の製造業における製品設計を念頭に置いた議論である。しかし、デジタル技術の威力は、化学産業などのプロセス系の製造業における製品設計にも及んでいる。
特に注目すべきは、情報科学を活用した研究開発である。このような手法は創薬研究の効率化が求められる製薬業界における「バイオインフォマティクス」に見られるように、研究開発を大きく前に進める可能性がある。例えば、創薬研究の臨床開発フェーズでは、ビッグデータ解析を通じて病気の発症や進行に密接に関係する遺伝子変異や生体分子「バイオマーカー」によるターゲットの絞り込みを行うことが有効になる。
そして、近年、同様の研究開発手法を素材分野へ適用する動きが活発化してきており、AI やビッグデータを素材分野に適用する、いわゆる「マテリアルズ・インフォマティクス」が注目を集めてきている。マテリアルズ・インフォマティクスは、もともとアメリカで始まり、2011 年のオバマ政権下で始まったマテリアルズ・ゲノム・イニシアチブ(MGI)が端緒と言われている。2012 年には、MGI に取り組む研究者らが、日本が発表した電池材料に関する論文情報をもとにインフォマティクス的な手法を活用して電池材料開発を行い、日本企業が実験的に見出した結果と同等の結果を論文発表した。これは、実験をせずにデータ分析のみで材料を導き出した点で非常に注目を集めた。
その他、欧州、中国、韓国等においても様々な取組が行われている。日本においても、2013 年に内閣府主導の戦略的イノベーション創造プログラム(SIP)において始まり、産学官連携による分野横断的な基礎研究から実用化・事業化までを見据えて一気通貫で研究開発を行っている。また、2015 年には文部科学省の情報統合型物質材料開発イニシアチブ(MI2I)において、各種材料の具体的テーマに取り組むとともに、データ駆動型の研究手法の開発に取り組み、産官学の研究者や技術者が研究開発の現場で活用できる情報統合型物質探索・材料開発システムの構築を行っている。
また、経済産業省においては、2016 年からの予算事業において、有機系の機能性材料の実験やシミュレーションによって創出したデータをマテリアルズ・インフォマティクスと融合し、革新的な機能性材料の創成・開発を加速させることを目指しており、2019
年4月にはシミュレーターの公開も実施した。
一般に、マテリアルズ・インフォマティクスの活用には、質の良い多くの技術データが必要と言われている。このような技術データとしては、民間企業が日々の研究開発活動の一環として独自に蓄積・保有しているものも多いが、学術論文や特許文献等の公知情報も技術データの宝庫であり、協調領域としてデータを整理することは有効であると考えられる。
特に特許情報の整理は民間企業の関心も高く、文献を技術分野ごとに整理することも可能であることから、2019 年 12月より、民間企業や公的研究機関とともに特許情報を活用するためのデータベースの構築及び持続的な活用のための仕組み作りの検討を開始した。
化学系企業など 20 者近い参画者が集まり、検討を進めている点において、これまでにないマテリアルズ・インフォマティクスに関する取組として高い注目を集めている。
このような施策の連携等を通して、世界において高いシェアを確保してきた機能性材料を始めとする素材分野において、研究開発現場でマテリアルズ・インフォマティクスを活用し、日本がその研究開発力を維持・強化できるように、必要な基盤構築を支援していく。
3 製造現場における5G等の無線技術の活用
(1)5Gとローカル5Gの動向
5G とは、ITU(国際電気通信連合:InternationalTelecommunication Union)が国際標準化を、3GPP(3rd Generation Partnership Project)が標準仕様策定をそれぞれ進める「第5世代移動通信システム」であり、「超高速通信」、「超低遅延通信」、「多数同時接続」を実現することがその特徴である。
具体的には、
最高伝送速度 10 Gbps(LTEの 100 倍、4G の 10 倍)
接続機器数 100 万台 /km²(LTE の 100 倍、4G の 10 倍)
超低遅延1ms(LTE、4G の 10 分の1)
が5G の主な要求条件として挙げられている。3GPP において5Gの仕様は「Release15」にて基本機能が策定され、Release16」以降順次機能が拡充される予定である(図 133-1)。
既に消費者向け市場については、米国や中国、韓国を始めとした諸外国においてスマートフォン向けの5G サービスが開始されており、日本においても 2020年3月に、NTT、KDDI、ソフトバンクの3社がサービスを開始した。楽天においても、2020 年以降にサービスが開始される予定である。
ローカル5G は、地域のニーズや多様な産業分野の個別ニーズに応じて、様々な主体が柔軟に構築・利用可能な第5世代移動通信システムである。
従来の移動通信システムはキャリア事業者を中心に公衆網として構築されてきたが、5G では公衆網としてのサービスに加え、ユーザーが電波免許を取得したエリアでの独自の運用が可能となる。ローカル5G のユースケースとして、医療機関や製造現場、スタジアム等、多様な場面での活用が想定されている。
日本においては、免許帯である 4.6-4.8GHz 及び28.2-29.1GHz の周波数帯がローカル5G の候補帯域として想定されており、先行して制度整備が行われた 28.2-28.3GHz の 100MHz 幅については、2019年 12 月より総務省への免許申請が開始された。
28.2-28.3GHz 以外の帯域についても、引き続き制度整備が進められる予定である。
(2)製造現場における5Gの活用の期待
製造現場における5G の活用を考える上では、通信システムの高度化の観点と、ローカル5G 等による無線技術の活用の2つの観点から、その可能性を捉える必要がある。
前者については、5G の実装は工場内等の閉域網やインターネットへとつながる通信システムを高度化することから、例えば、新たなアプリケーションの開発を通じたエッジコンピューティングやクラウドコンピューティングの活用拡大による生産性向上が期待される。
ローカル5G 等による無線技術の活用の観点からは、現場の作業支援が期待されており、例えば、産業機械のリアルタイムでの遠隔操作や遠隔からの保守点検、多くの無人搬送車の活用は、人手不足に直面する製造現場を支援するものとして期待がされている。また、工場における無線化が進むことで産業機械のワイヤレス化が実現すれば、レイアウト変更に伴う配線コストが軽減されるため、より柔軟な製造ラインの構築が可能となると考えられる。
以上のように5G によって製造現場における新たな可能性が期待される一方で、ユーザーである製造現場としては、4G や無線 LAN 等の無線技術の活用も視野に入れつつ、ユースケースとコストに応じて、どのような無線技術を活用するか検討する必要がある。
(3)製造現場におけるローカル5G等の無線技術の活用に向けた課題
工場においてローカル5G 等の無線技術を最大限活用するためには、製造システム特有の通信要件への対応や、通信障害の克服等が大きな課題となる。
例えば、無線 LAN 等が使う免許不要帯においては、既に製造現場において複数の IoT 機器が導入されつつあり、このような機器が発する電波が同じ周波数を利用する場合、互いに干渉し合うことで通信障害が生じ、その可能性を最大限引き出すことができなくなる可能性がある。
このようなことから、国立研究開発法人情報通信研究機構(NICT:National Institute of Informationand Communications Technology)では、「FlexibleFactory Project」を通じて、多種多様な無線機器や設備をつなぎ、安定して動作させるためのシステム構成である SRF(Smart Resource Flow)無線プラットフォームの研究開発を実施しており、非営利の任意団体であるフレキシブルファクトリパートナーアライアンス(FFPA:Flexible Factory PartnerAlliance)の活動を通じて、標準化活動が推進されている。
この他、通信干渉を回避し、無線技術を最大限活用するためには、「どの周波数帯域」を「どのような経路・回線」で、「いつ・どのように活用するか」という無線通信ネットワークの設計・運用や、「無線通信がどのように使われているか」を現場の管理者が把握することが重要となる。このため、ローカル5Gに限らず、多種多様な無線技術が今後益々製造現場に導入される場合、このようなノウハウの有無が企業の競争力に影響を及ぼすことが想定される。
(4)5G等の無線技術に対する国内製造業の認識
以上で確認したように、企業の競争領域として開発が進められている新たな無線技術に対して、国内製造業がどのように認識しているかを確認したところ、過半数は5G 等の次世代通信技術に「関心がある」と回答したものの(図 133-2)、「関心が無い」層にその理由を尋ねると「自社には関係が無い」「ビジネスへのインパクトがわからない」と考えていることが分かった(図 133-3)
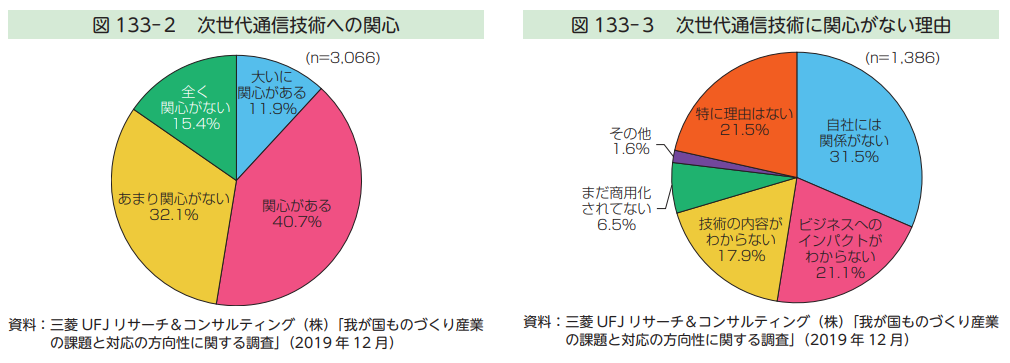
一方で、工場の無線化に対しては、「すでに一部導入している」割合が 27.7%に上り、さらに、全体の約4分の3が何らかの関心があると回答した(図133-4)。
従業員規模別に分析すると、規模が大きくなればなるほど工場の無線化に積極的で、従業員数1,000 人以上の大企業では過半数がすでに一部導入している(図 133-5)。
工場の無線化を始めとする無線技術の活用に伴う課題や不安としては、「セキュリティの確保」や「初期コストの不透明感」が上位に挙がる結果となった(図133-6)
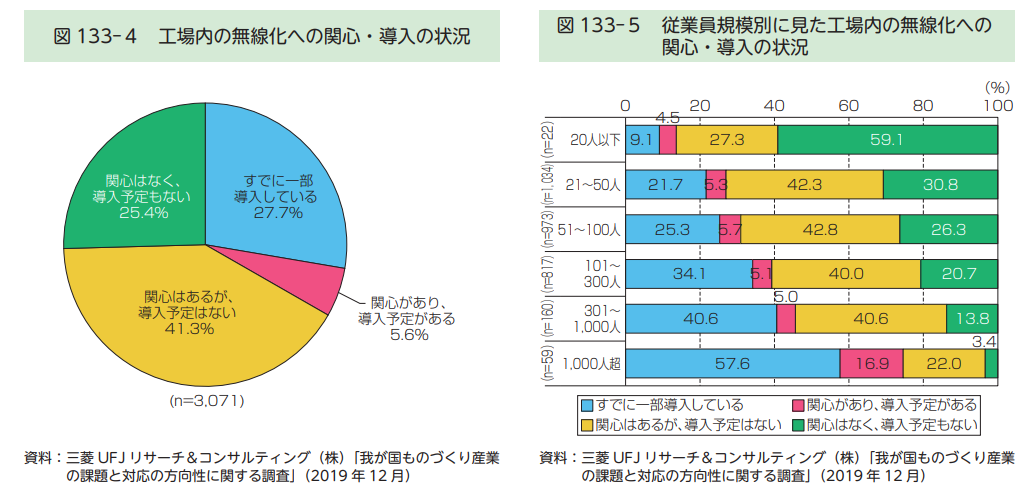
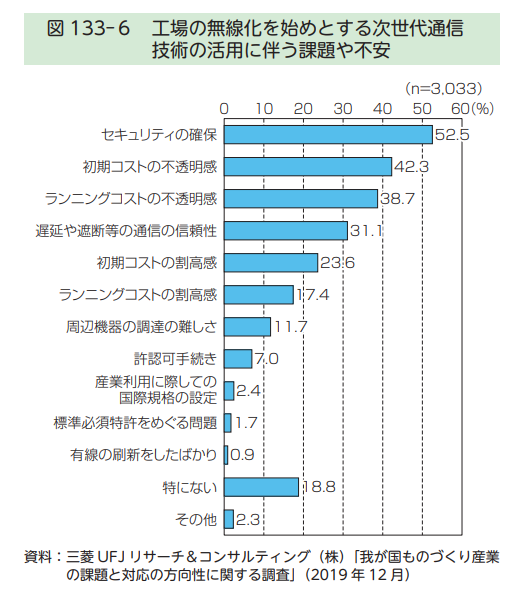
(5)SEP(標準必須特許)を巡るリスクの増大
近年、IoT により、様々なインフラや機器がインターネットを通じてつながり合う「第四次産業革命」と称される変化が国内外において急速に進展しているか、これらを提唱している。
その一方で、機器間の無線通信に係る標準規格の実施に必要な「標準必須特許」(Standard Essential Patent.以下「SEP」という。)を巡るライセンス交渉が問題となっている。
従来、情報通信技術の SEP を巡るライセンス交渉は、通信事業者間を中心に行われてきたことから、同じ業種の事業者同士では、互いに相手が保有する特許の権利範囲、必須性、価値を評価しやすいため、当事者間でロイヤルティについての合意は比較的容易であった。しかし、IoT の浸透により、今後は、標準必須特許権者と通信事業以外の業種の事業者との間で SEP のライセンス交渉が増加すると考えられる。
特にパソコン、ゲーム機、自動車、建設機械、インテリジェントビル等、多数かつ複数の部品を含むマルチコンポーネント製品に関しては、通常、各部品から最終製品に至るまで階層別にそれぞれの製造企業が存在し、階層的なサプライチェーンを構成している。
このようなマルチコンポーネント製品に係る業種の事業者と、情報通信技術に係る標準必須特許権者との間では、ライセンス交渉の慣行やロイヤルティについての相場観が大きく異なるため、SEP のライセンス交渉や紛争に関するリスクが著しく高まっている。特
に中小企業においては、SEP のライセンス交渉や紛争に関するリスクは、非常に大きなものとなるおそれがある。
しかも、SEP は、標準規格に組み込まれているがゆえに、ライセンスを受けないという選択肢がないため、実施者の交渉上の地位は SEP でない場合に比べて圧倒的に弱くなるため、SEP には標準化団体による方針(IPR ポリシー)により、公平・合理的・非差別
的(Fair, Reasonable and Non-Discriminatory。以下「FRAND」という。)という条件が定められている。しかし、SEP のロイヤルティに関する適切な算定の考え方については、依然として論争中である。
IoT が様々な産業分野に浸透し、国民生活に恩恵をもたらそうとしている中、SEP のライセンス交渉を巡るリスクが高まることは、IoT に関する投資を困難にし、標準必須特許権者と実施者の双方に不利益をもたらすだけでなく、経済社会の発展を阻害しかねない。
近年、標準必須特許を巡る紛争は深刻さを増しており、すでに、各国で裁判がいくつも起こされている(図133-7・8)。しかし、標準必須特許を巡る係争について、我が国製造業企業を対象にアンケート調査を行ったところ、9割近い企業が「全く知らない」「あまり知らない」と答えており、この問題に関する認識が著しく低いことが明らかとなった(図 133-9)
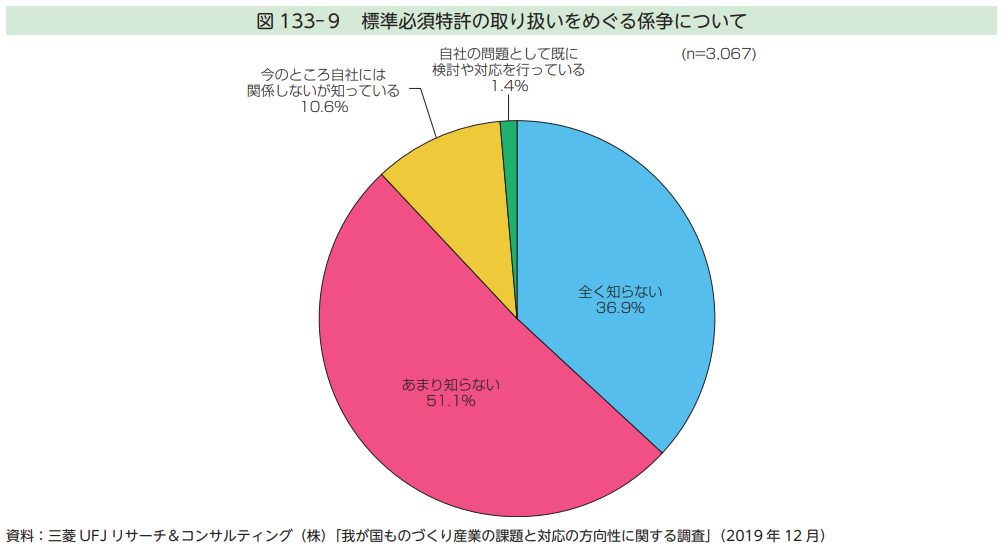
このようなことから、経済産業省特許庁では、2018 年6月、標準必須特許を巡る紛争の未然防止及び早期解決を目的とする「標準必須特許のライセンス交渉に関する手引き」を公表した。また、経済産業省は、「マルチコンポーネント製品に係る標準必須特許のフェアバリューの算定に関する考え方」を公表したところである(コラム参照)。
3.中小企業に対する注意喚起
IoT が経済社会に浸透するに従い、中小企業が IoT を活用する事例も増加していくことから、今後は標準必須特許権者と中小企業との間で SEP のライセンス交渉や紛争が増加することが予想される。
しかし、中小企業は、標準特許権者や大企業に比べて専門人材や交渉に関する情報等、対応に必要なリソースが不足しているため、不合理な条件でライセンスを締結するリスクがより高い。このため、中小企業に対して、特許侵害訴訟や差止請求権の威迫を背景に、不当に高額なライセンス料や和解金を得ようとする者が現れる恐れもある。
そこで、中小企業が標準必須特許権者から警告書等によりライセンスの要求を受けた場合には、まずは、知的財産権の専門家に相談し、適切な対応を検討することが望ましい。
その際、独立行政法人工業所有権情報・研修館(INPIT)の知財総合支援窓口等、公的な機関の相談窓口を利用するという方法もある。
なお、特許庁「標準必須特許のライセンス交渉に関する手引き(以下「手引き」と言う。)」(平成 30年6月5日)は、標準必須特許権者による以下のような行為は、不誠実な交渉と評価される方向に働く可能性があると指摘している。
(1)実施者に警告書を送付する前、送付してすぐに又は交渉を開始してすぐに、差止請求訴訟を提起する
(2)実施者にライセンス交渉を申し込む際に、SEP を特定する資料、クレームチャート等の請求項と標準規格や製品との対応関係を示す資料について、実施者が標準必須特許権者の主張を理解できる程度に開示しない
(3)機密情報が含まれていないにもかかわらず、実施者が秘密保持契約を締結しない限りクレームチャート等の請求項と標準規格や製品との対応関係を示す資料を実施者に提供できないと主張する
(4)検討のための合理的な期間を考慮しない期限を設定した申込みをする
(5)実施者に対し、ポートフォリオの内容(ポートフォリオがカバーする技術、特許件数、地域など)を開示しない
中小企業は、SEP のライセンスの要求を受けても、慌てて要求に応じるのではなく、標準必須特許権者が以上のような行為を行っているか否かを十分確認した上で、適切に対応することが望ましい。また、その後、必要となる標準必須特許権者との交渉の進め方についても、「手引き」を参照して進めることが適切である。
4 製造業のデジタルトランスフォーメーションに求められる人材
我が国製造業における人手不足状況は年々深刻化しており、ますます大きな課題となっている。過去のものづくり白書においても、度々同問題に触れ、デジタル化を通じた解決を模索してきた。ここでは、本節で論じてきたデジタルトランスフォーメーションを実現するために必要となる人材について、更に分析を深める。
(1)製造業のデジタル化に必要な人材とその確保状況
①我が国製造業における人材確保の状況
はじめに、我が国製造業における人材確保状況を概観する。本章第1節で確認したとおり、2020 年3月時点での完全失業率は引き続き3%を下回る低水準で推移しており、低下傾向が続いている。
一方、有効求人倍率は 2018 年4月から 2019 年6月までの間1.6 倍を超える高水準が続いてきたが、その後は低下傾向となっており、2009 年以降回復が続いていた有効求人倍率に変調が見られる結果となった(前掲:図111-19)。
製造業の従業員不足感は、2014 年以降「過剰」と答える割合を「不足」と答える割合が上回り、マイナスが続いているものの、2019 年第1四半期から 2020 年第1四半期にかけては、大企業、中小企業共にマイナス幅が縮小傾向である。(図 134-1)。
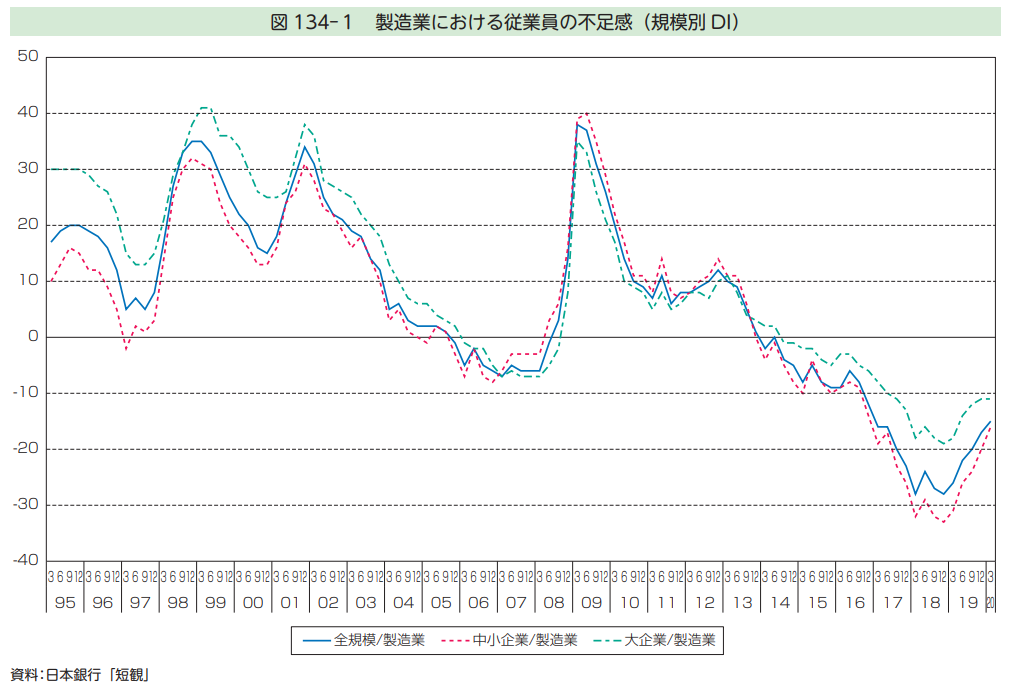
②デジタル化に必要な人材
アンケートにおいて工程設計力が低下した理由を尋ねると、79.4%が「ベテラン技術者の減少」、19.1%が「間接部門の人員削減」と回答しており、ベテラン技能者の退職や人材不足は、エンジニアリングチェーンにも深刻な影響を与えていることが分かる(前掲:図 132-8)。
一方、工程設計力が向上した理由を確認すると、「生産技術、製造、調達といった他部門との連携強化(79.2%)」「営業、アフターサービスなどから顧客ニーズのフィードバックを強化(26.5%)」「デジタル人材の育成、確保(22.5%)」が上位に挙がっており、デジタル人材の活躍による部門間連携がエンジニアリングチェーンの強化に有効であることが示唆される(前掲:図 132-7)。
一方で、デジタル人材の供給は十分に進んでいない。「IT 人材白書 2019(独立行政法人情報処理推進機構)」の中で IT 企業やユーザー企業に対して行われたアンケートによれば、特に IT 人材の「量」の不足感が強まっている状況が確認できる(図 134-2)。
デジタル技術を理解している IT 人材の質・量両面での供給不足は、デジタル化によるエンジニアリング チェーンの強化に向けた課題の一つである。
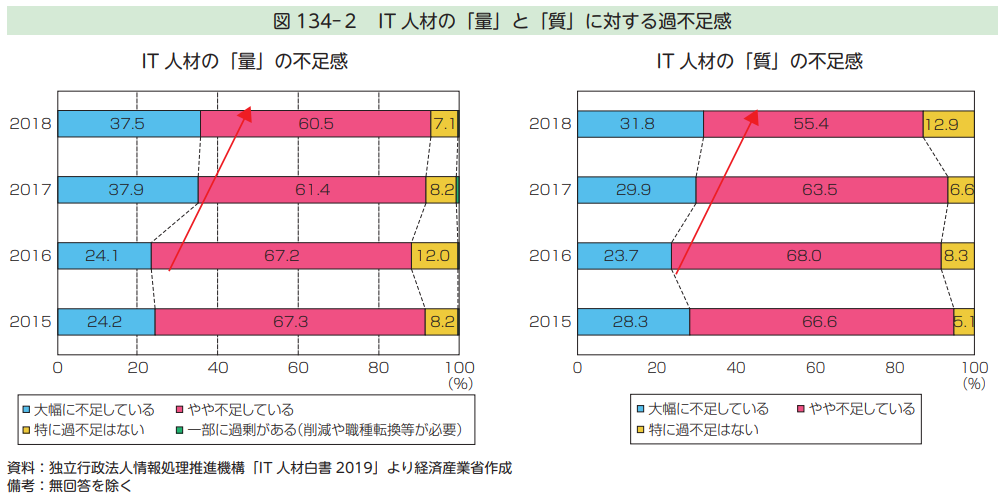
③システム思考の強化
エンジニアリングチェーンを強化するためには、各部門の個別最適ではなく全体最適を考慮してビジネス全体を俯瞰する能力も重要となるが、この能力は「システム思考」と呼ばれている。
システム思考は「システムズエンジニアリング(システム工学)」として体系化されており、複数の専門分野にまたがる事象を統合し、統合された事象全体としてのシステムを成功させるために必要となるアプローチと手段を構築する力を指す。
米国において汎用化されたもので、軍事産業、航空・宇宙産業などの隆盛に伴って大規模システムを設計し、運用するために必要不可欠な教育として同国で発展してきたとされる。
我が国における製造業のデジタル化は個別最適に陥ることが多く、システム思考を強化することが重要であると過去のものづくり白書においても繰り返し述べられてきた。
このようなシステム思考は、米国において体系化されたものであるが、その一方で、システム思考は、「チームでの協働(協創)」という点において、日本的手法とされる「ワイガヤ」や「スリアワセ」と共通するという指摘もある。
しかし、2.(2)において指摘したように、我が国製造業における部門間の連携は必ずしも十分とはいえない状況にあり、システム思考に必要な「チームでの協働(協創)」の妨げとなっている。
したがって、部門間を越えたデータ連携を進め、バーチャル・エンジニアリング環境を整備することは、「ワイガヤ」や「スリアワセ」といった「チームでの協働(協創)」を復活・発展させ、我が国製造業におけるシステム思考の導入を容易にするものと考えられる。
なお、システム思考は、現在、国内では慶応大学大学院システムデザイン・マネジメント研究科などを中心に講座提供されており、多くの卒業生が輩出されている。部門間のデータ連携やバーチャル・エンジニアリング環境の整備と平行して、このようなシステム思考のできる人材を育成することで、エンジニアリングチェーンを強化していくことが重要であろう。
(2)数学―製造業のデジタル化に必須の知識
今後、製造業においてデジタルトランスフォーメーションが進み、IoT、AI 等のデジタル技術が活用されるようになっていくに従って、これまで以上に必要性と重要性が増してくると思われる人材は、数学の知識や能力を有する人材である。
例えば、数学の能力は、デジタル化した製造業に不可欠なデータ分析、モデリング、シミュレーションにおいて大いに発揮される。特に AI と人間との協調・協働においては、数学が AI の制御を始め、学習データや推定結果の信頼性を高めるために必ず必要とな
る。
さらに、AI 自体に画期的な技術革新を起こすともなれば、高度な現代数学の能力が決定的に重要になるであろう。AI 以外にも、VR、AR、マテリアルズ・インフォマティクス(MI)、量子暗号や量子コンピュータ等、製造業に大きなインパクトをもたらすと予想されるデジタル技術革新の多くが、高度な数学の能力を要するものである。
また、数学は「モノや構造を支配する原理」を見出すための普遍的かつ強力なツールであり、数学の力によって、将来の変化が起こる前の予兆の検出、予測の精緻化、ビッグデータを重要な部分にのみ着目して活用することなどが可能となる。
この数学の能力は、ダイナミック・ケイパビリティの要素の一つである「感知」を格段に強化するものであろう。
加えて、(1)において述べたように、今後は、全体最適を考慮してビジネス全体を俯瞰するシステム思考が重要性を増してくる。言い換えれば、具体的な課題を抽象化・一般化することによって俯瞰し、統合的に解決する能力が以前にも増して求められることになるが、その抽象化・一般化において、数学的な思考は大きな力を発揮する。
さらに、数学は、ライフサイエンス、ナノテクノロジー、環境科学、材料科学、物理学、化学、金融工学、経済学、社会学など様々な分野の科学技術の基盤となるため、数学の進歩は各分野の発展をもたらすほか、数学を軸とすることで異なる分野の課題を共通化し、分野融合的な技術開発が可能となる。ダイナミック・ケイパビリティ論に従っていうならば、数学は、異なる分野の知識を融合させて新たな価値を生み出す「共特化」を可能にするものである。
このように、製造業のデジタル化を進め、そのダイナミック・ケイパビリティを強化する上で、数学の知識や能力を有する人材が非常に重要になると考えられる。
そこで、我が国における数学の水準について見てみると、数学研究についていえば、若い数学者の優れた業績を顕彰するフィールズ賞の受賞者数(3名)では、我が国は、世界第5位である。また、2006 年に伊藤清(京都大学名誉教授)が、ガウス賞(社会の技術的発展と日常生活に対して優れた数学的貢献をした研究者に贈られる賞)の第1回受賞者となっており、さらに、2018 年には柏原正樹(京都大学名誉教授)が、チャーン賞(生涯にわたる群を抜く業績を上げた数学者に贈られる賞)の第3回受賞者となっている。
そして、これらの賞を授与する国際数学連合(IMU)の総裁を 2018 年まで4年間務めたのが、フィールズ賞受賞者でもある森重文(京都大学高等研究院長)である。このようなことから、我が国における数学の研究能力の水準は、他国に引けをとるものではないといえる。また、義務教育終了段階(15 歳児)の生徒が知識・技能をどの程度活用できるかを評価した「経済協力開発機構(OECD)」の調査(PISA)によると、我が国の科学的リテラシーや数学的リテラシーは、国際的に見ても上位にあり、高いポテンシャルを持つことが分かる。さらに、高校生等が参加する「国際数学オリンピック」や「国際情報オリンピック」では、例年メダリストを輩出し、国際順位も上位にある。
なお、経済産業省が実施した「産業振興に寄与する理工系人材の需給実態等調査」では、2017 年度採用予定人数と 2019 年度の採用希望人数を比較すると、全体的にはマイナス 7.7%と採用希望人数が減少している中で、人工知能(プラス 125.0%)や web コンピューティング(84.7%)に加えて、統計・オペレーションズ・リサーチ(プラス 90.9%)や数学(プラス 69.2%)の割合が増加しており、我が国の企業が理数系人材の獲得に動いていることが明らかとなっている。
しかし、製造業において数学の知識や能力を有する人材を活用する上では、課題もある。その一つは、我が国の若手数学者のうち、民間企業に進む者が比較的少ないということである。
図 134-3・4・5のとおり、我が国において、数学の博士後期課程を修了した者の進路状況については、修了後に高等教育機関に進むものが多く、民間企業等に進む者は 2013 年から 2016 年にかけて増加しているが、全体の 12%程度となっている。
一方で、「American Mathematical Society」の調べによると、アメリカの PhD(数理科学)修了者数は、ここ数年増加傾向にあり、なかでも産業界へ進む者が年々増え、2016 年には全体の約 30%となっている(図 134- 6)。アメリカの動向で注目すべき
は、PhD 修了者の数が日本の 10 倍以上である上に、産業界へ進む PhD 修了者が増えている一方で、学術界に進む PhD 修了者は必ずしも減っているわけではないという点である。
今後、我が国においても、若手数学者が、学術界のみならず製造業においても活躍できる機会が拡大することが望ましい。
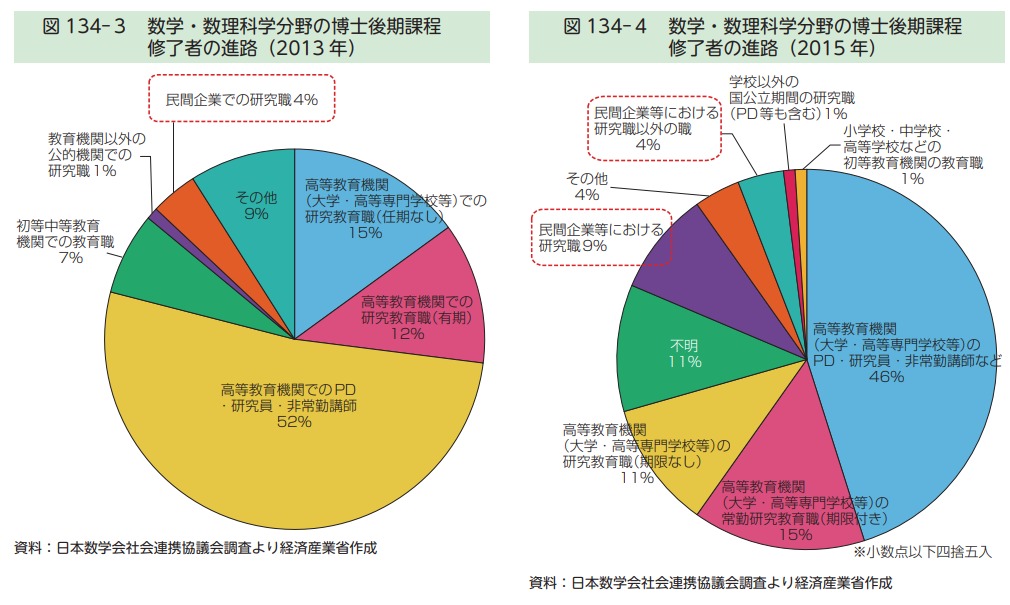
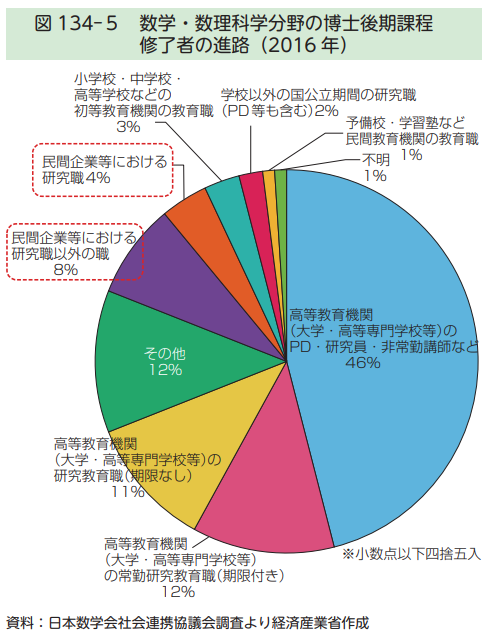
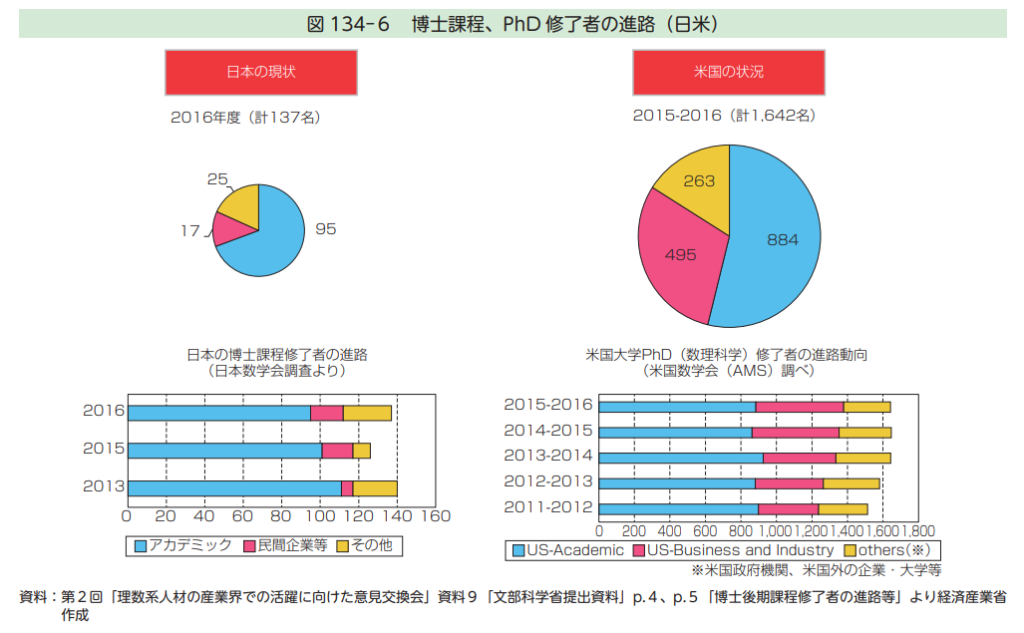
出典 経済産業省 第3節 製造業の企業変革力を強化するデジタルトランスフォーメーション(DX)の推進
関連ページ
VUCA (ブーカ)
VUCA(ブーカ) 関連資料 不確実性 総論
VUCA(ブーカ) 関連資料 詳細
デジタル技術を徹底的に利活用することについて、自動車メーカー向けの車載電子機器のOEM開発・設計・大量生産や多品種少量生産・品質・フィードバックなど、製品として取りまとめる役割のPM(プロジェクトマネージャー)と30年以上モノづくりをやってきた優日堂がお手伝いさせていただきます。
また、モノからコトへ、製品を伴う新規事業戦略の立案のコンサルティング、アドバイザーも承っております。
お気軽にお問い合わせください。090-1050-5159受付時間 9:00-17:00 [ 土・日・祝日除く ]
info@yuhidou.com